Press & Downloads
Search and find: Press reports as well as publications and downloads that we have compiled for you.
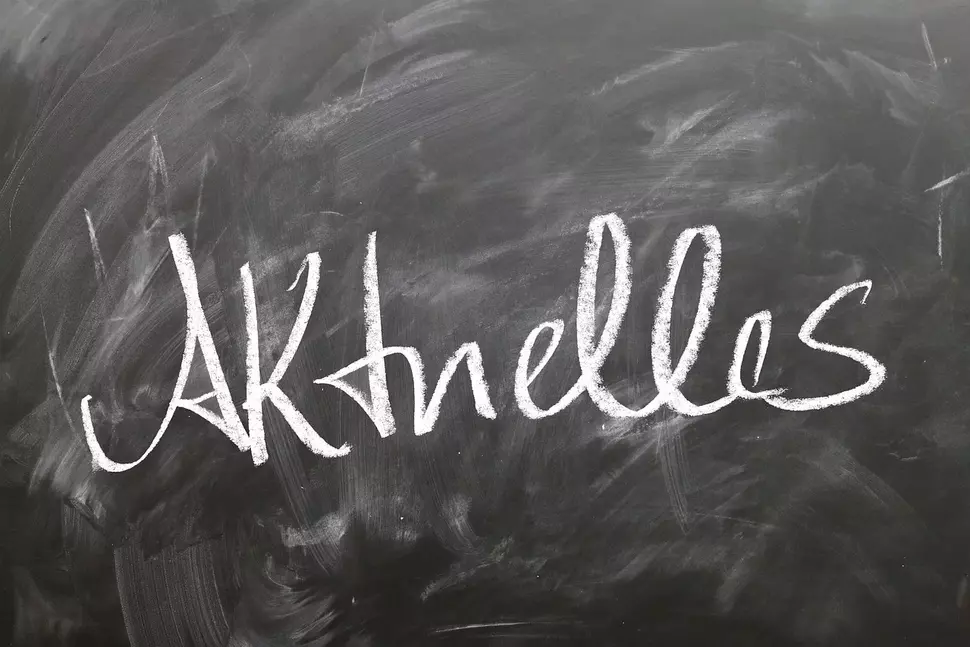
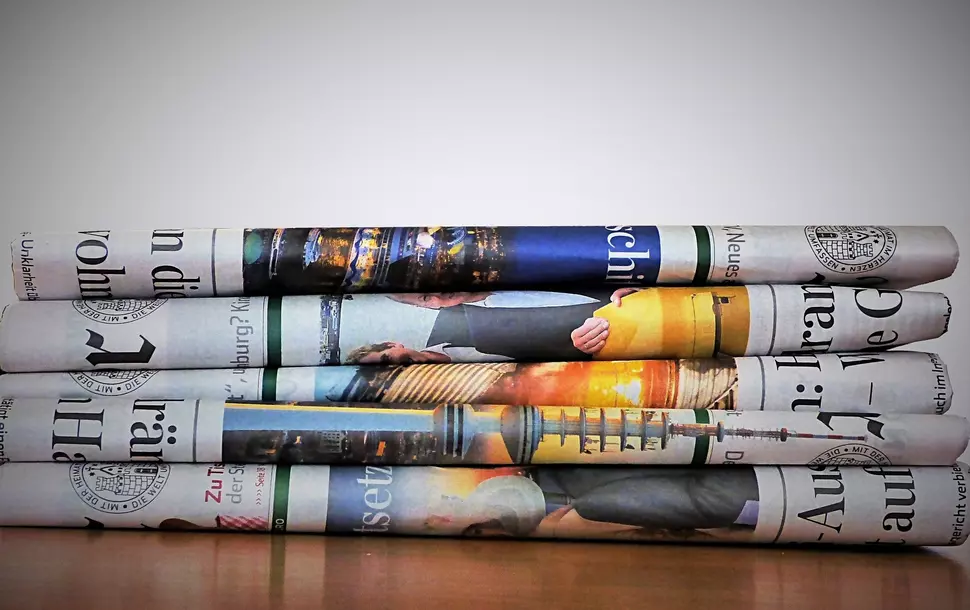
Information for Media Representatives
Together with our experts, we are happy to support you with journalistic questions about our work and our tasks. Our aim is to provide you with the relevant facts and information as comprehensively, quickly and up-to-date as possible.
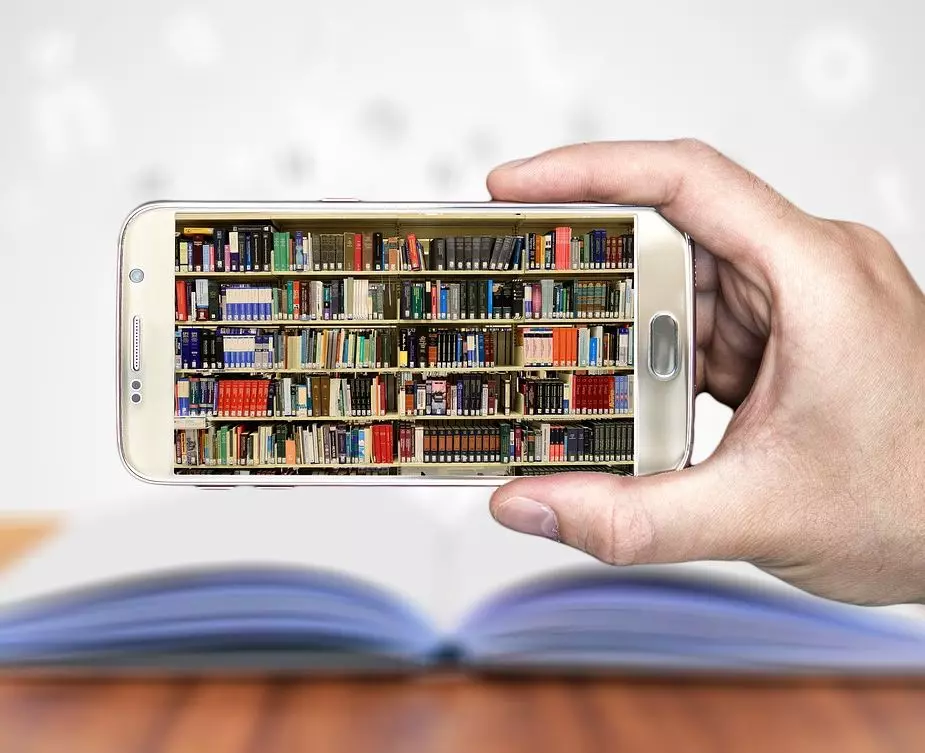
Publications & Downloads
The Saxony Trade & Invest Corp. (Wirtschaftsförderung Sachsen GmbH - WFS) publishes a range of brochures, flyers, presentations, information sheets, etc. that present Saxony as a business location, selected sectors and the work of WFS.
Your contact persons
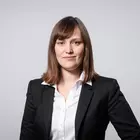
Danisch, Désirée
Désirée Danisch
Industry, Innovation & Marketing
+49-351-2138 251
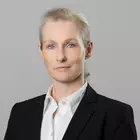
Golde, Katrin
Katrin Golde
Industry, Innovation & Marketing
+49-351-2138 252
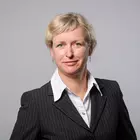
Lange, Sandra
Sandra Lange
Industry, Innovation & Marketing
+49-351-2138 255
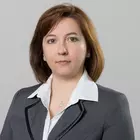
Susan Pietzsch
Industry, Innovation & Marketing
+49-351-2138 250