BMW Plant Leipzig: Sustainability Pioneer
The BMW Plant Leipzig, which opened in 2005, is one of the most modern and sustainable car factories in the world. It is also a pioneer when it comes to electromobility: the BMWi3, the world's first premium vehicle designed from the ground up for electric drive, was launched on the road from here.
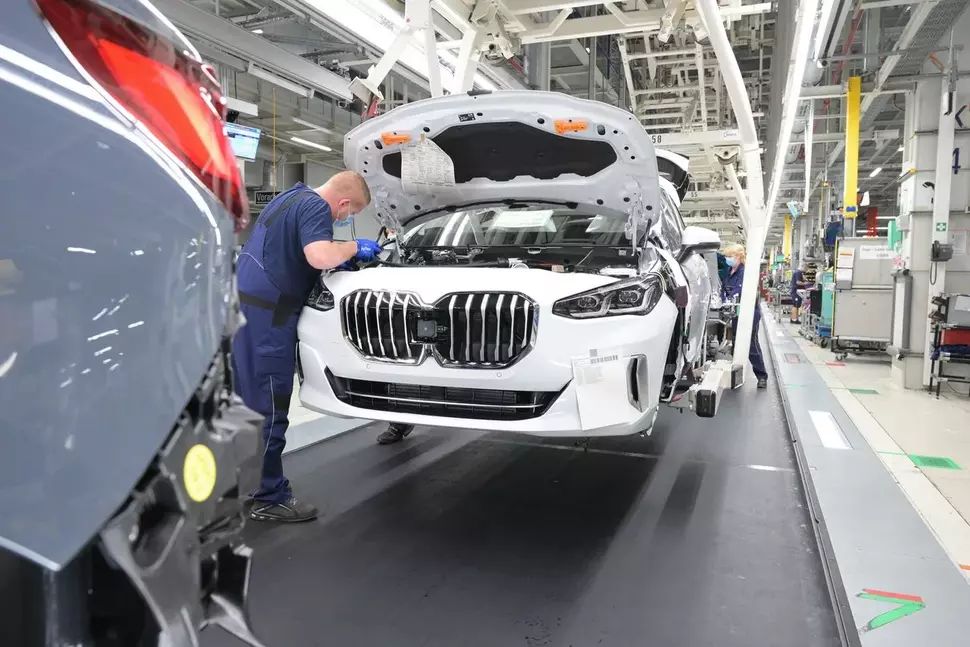
Infomodul
Facts about the BMW plant in Leipzig
-
March 2005
Start of series production -
About 5,700
Employees (2023) -
More than 4,000 million euros
Total investment ammount -
More than 1,000 vehicles
daily production
Milestones
The history of BMW’s automobile production in Saxony began in 2001. The Bavarian automobile manufacturer was looking for a European location to produce its planned 1-series. From a list of 250 locations, the decision fell in favor of Leipzig. The combination of many positive factors which were available here, such as the industrial experience of the people in Saxony, the well-developed infrastructure, the opportunities for organizing flexible structures as well as the favorable location within the network of BMW production sites led to this decision.
The groundbreaking ceremony was held in 2002. 2005 marked the start of mass production: Initially with the 3-series sedan; and as of 2007, with several models of the brand-new 1-series. Starting in 2013, BMW cars of the 2-series were also built in Leipzig. In 2014, another innovation followed: The 2-series Active Tourer was the first BMW with front-wheel drive produced in Saxony.
Today, about 1,000 vehicles powered by combustion engines and hybrid drives leave the assembly line in the Leipzig Plant every day. Currently, the permanent staff of about 5,700 employees produces the BMW 1-series, the BMW 2-series Gran Coupé as well as the BMW 2-series Active Tourer. In February 2023, the employees celebrated a special jubilee – the 3,333,333rd BMW “Made in Leipzig” was produced since the start of mass production.
So far, the BMW Group has invested a total of more than four billion euros into the production site.
BMW Plant Leipzig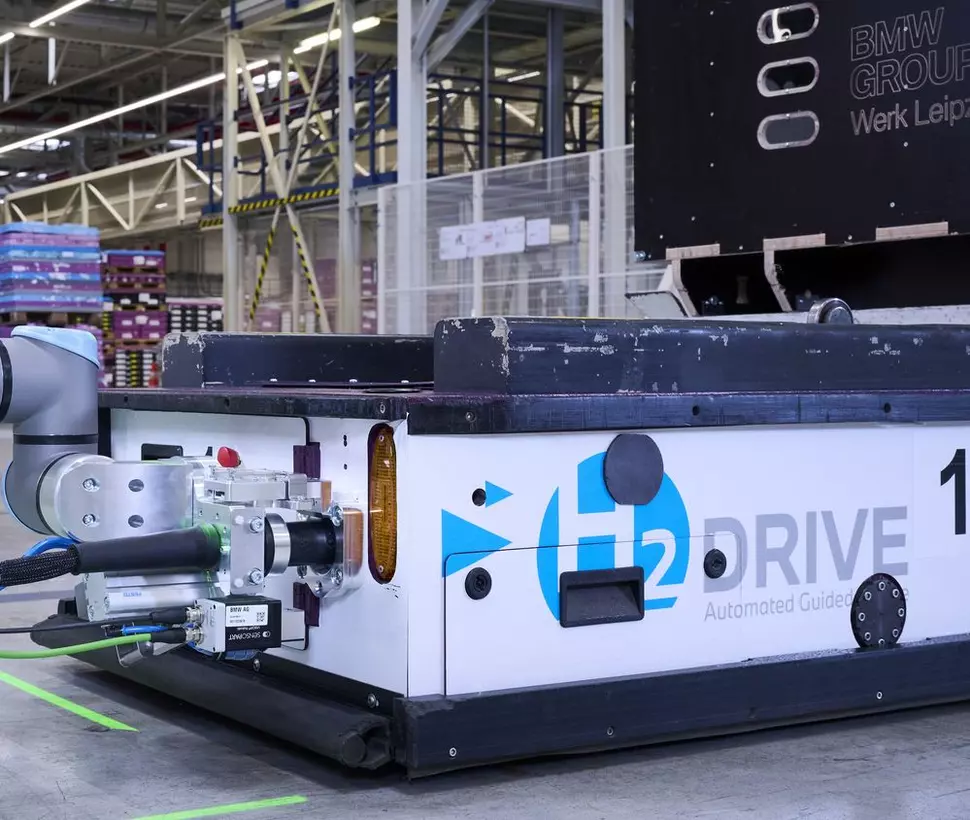
Sustainability in Production and Product
The investment not only helped to continuously expand and modernize the production capacities in the pressing plant, car body shop, paint shop, and assembly line. BMW also meets the objectives which the company has pursued in Leipzig right from the start; namely, to advance and promote the topic of sustainability in a holistic and comprehensive approach. This is best exemplified by wind turbines, a battery storage farm for the secondary use of worn-out e-vehicle batteries and energy-efficient processes as well as by pilot projects revolving around the use of hydrogen in production and logistics.
Four wind turbines have become the trademark of the BMW Group’s Leipzig Plant. Already since 2013, the wind power stations have been an icon of the factory. BMW was the first German automobile manufacturer to install this technology to supply a plant with electricity which marked the start of a sustainable value creation process. Starting in 2013, the green energy had initially been used to produce the BMW i3 and i8 series. With the i3, BMW brought the world’s first premium electric vehicle on the road which was designed solely and entirely for this type of propulsion. And for the manufacture of this vehicle, carbon-fiber reinforced plastics (CFRP) were used for the first time ever in automobile mass production. Until the end of production in mid-2022, which had been extended several times, more than 250,000 i3 cars left the Leipzig Plant and headed for their customers around the entire globe. What also stands for BMW’s start into the era of electromobility and intelligent lightweight construction is the plug-in sports car i8. 20,500 vehicles of this model type were built between 2014 and 2020.
BMW is the world’s first automobile factory to apply in its paint shop in Leipzig a newly developed burner technology which permits hydrogen and natural gas to be used either alone or in a mixture. With the pilot run of a double furnace, the plant is testing the feasibility of reducing the CO2-intensive use of the fossil fuel natural gas. A vital prerequisite for the continuous use of hydrogen is the sufficient grid-bound availability of green hydrogen. Towards this end, the Leipzig Plant will have the opportunity of using a hydrogen network that is currently emerging in the region. When it comes to factory logistics, hydrogen has been used as an energy carrier already for many years now. In 2013, Germany’s first indoor hydrogen filling station was built on the factory premises in Leipzig. Forklift trucks and tugger trains used in intralogistics can be refueled there. Today, almost ten years later, the Leipzig Plant has more than 130 fuel-cell powered forklifts which is Germany’s largest fleet. For the continued development of these drive systems, BMW also relies on Saxony’s expertise. Together with the vehicle developer FES from Zwickau, driverless transport systems are being developed which run on hydrogen-powered fuel cells. Fuel for the entire fleet is provided by five indoor hydrogen filling stations on the factory premises; the youngest of which permits for the first time ever fully automated refueling processes.
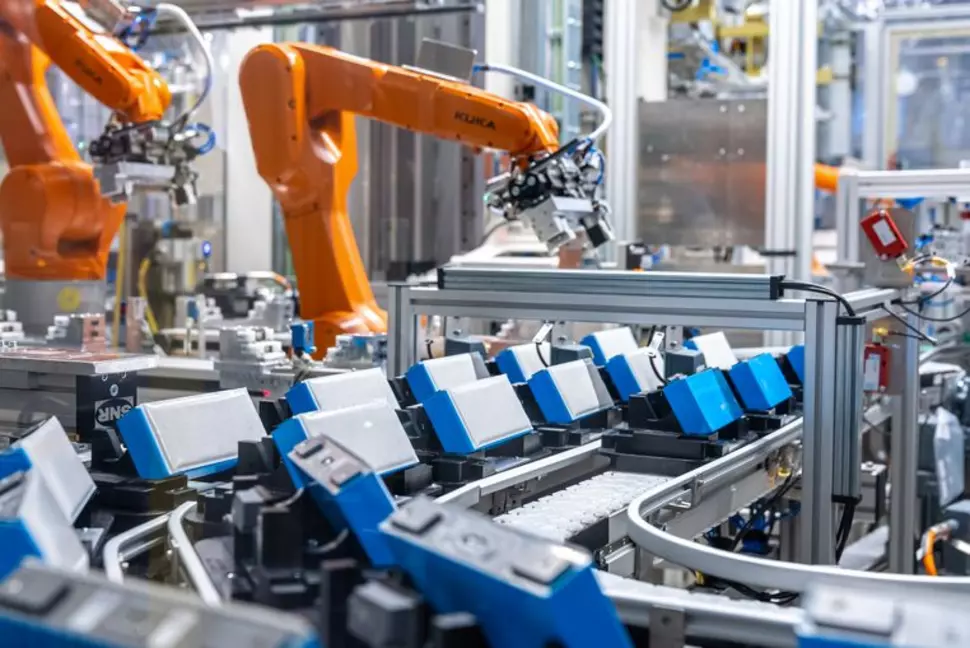
Production of High-Voltage Batteries
When it comes to accelerating sustainable mobility, BMW underpins the pioneering role of its Leipzig production site with the latest investments. For an amount of 800 million euros, the automobile manufacturer is expanding the production of battery components in Saxony. The vacated floor space of the former i3 production as well as the extensive experience of the staff gained from e-vehicle production all provide the best possible prerequisites here. A total of ten new production lines will be set up by 2024, which include three battery module lines, five lines for the coating of cells as well as two high-voltage battery assembly lines.
Part of the high-voltage batteries made in Leipzig are used directly on site because they are built into the fully electric Mini Countryman which will be manufactured in Saxony as of 2024. This will be the first Mini model to be built completely in Germany. The new crossover model of the Mini brand will leave the assembly line in Leipzig both with a combustion engine and a fully electric drive. Thus, the Saxon factory demonstrates once again its high flexibility. It is the first factory where vehicles of the BMW and Mini brands are produced together. The systematic orientation towards comprehensive and holistic sustainability was one reason for the company to locate the production of the new Mini Countryman in Leipzig.