Customized Automation Solutions for Small and Medium-Sized Enterprises
The training and application center of the ICM - Institut Chemnitzer Maschinen- und Anlagenbau investigates and develops new concepts for the implementation of collaborative assembly systems. A number of SMEs have already been able to see the positive effects for themselves.
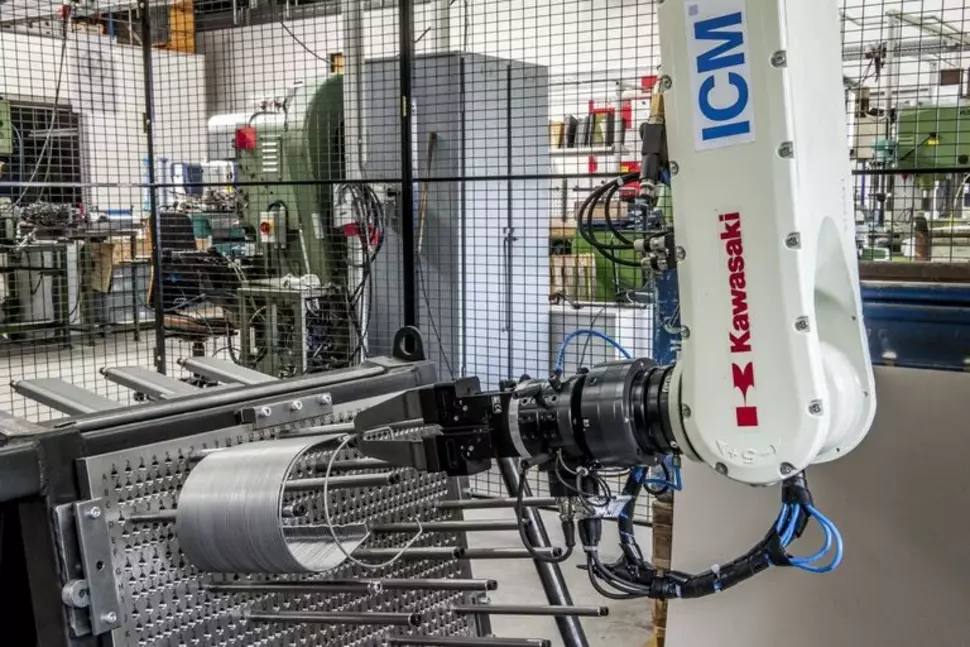
Whenever Marcel Ott comes to a customer, then not only the supervisor can’t wait to hear his proposed solutions. The employees also look forward to hearing them – even though he often reorganizes their familiar workplaces. The software developer works in the automation/robotics sector at the ICM – Chemnitz Institute for Machinery and Plant Construction. Since its official opening in November 2019, a training and application center abbreviated as SchAz has also been part of the institute. The center evolved from a project funded by the Federal Government which focuses on the investigation of new concepts for the implementation of collaborative assembly systems.
The positive effects have already convinced a large number of small and medium sized entrepreneurs. All of them have similar problems – irrespective of their individual branches and products. “The companies have to cope with high flexibilization and cost pressures. With conventional working methods, they often reach their limits. The unavailability of the required labor force assumes an increasing role as well,” explains Marcel Ott.
For example, the Bader Glastechnologie GmbH in Klipphausen: The company assembles glass panes of various sizes into modules for the most diverse needs and requirements. So far, the fitting and bonding into sheet metal profiles has required physically demanding manual work. The ICM automation experts have developed a manufacturing cell which is flexible in its use; those who operate the cell only need to put on the sheet metal stencil, and all other production steps such as sampling the right glass size, applying the glue bead, bonding glass and metal, and finally discharging the finished product from the cell are all carried out automatically. The plant operators select the appropriate glass type which is required and position the glue beads from a panel. Thus, new products can be integrated without a lot of effort. The benefits speak for themselves: “This solution ensures stable processes and a consistent product quality with high dimensional accuracy. And the output is also increased,” Marcel Ott names just some of the benefits. And this should not be ignored either: “The employees are glad that they don’t have to carry out stressful, monotonous activities and are instead able to focus on other, more sophisticated tasks. The robot has lost its reputation as a job killer.”
This is also demonstrated by the next example. The Bahner Schäfer GmbH located in Oelsnitz in the Erzgebirge Mountains manufactures technical springs. So far, the end sections of bent wire parts have been handled and machined by hand, which means that the parts fell into a box but were only deburred on one side so that they still had to be “disentangled” and machined on the other side. The ICM team has implemented the requisite concept with which a robot removes the diverse parts with the help of various gripping tools and deposits and/or suspends them for further processing in a predefined manner. The previously manual deburring has been automated as well. “One of the challenges was to integrate the solution into the production hall without obstructing any existing transport routes in such a way that flexible work is still possible with the system. This was attained through a robot portal on the ceiling and a foldable fence,” explains Marcel Ott. He points out that particularly those automation solutions which are to be integrated into existing production halls and cater to the specific needs and requirements of smaller enterprises cannot be taken off the shelf. “We always look at the entire process including the respective upstream and downstream activities before we develop together with our customers the requisite solution that suits them in each individual case. Just the robot alone is not enough. It is essential to pursue a comprehensive, holistic approach so that such integration leads to the desired effects. Technologically clean and economically viable, these are the decisive criteria for each and every project,” outlines the automation expert.