Robotics from Saxony as a Blueprint for Europe’s Microelectronics
Automation solutions from Saxony are making a significant contribution to future-proofing the German chip industry. Infineon Technologies, for example, successfully mastered post-automation in its 200 mm production facility in Dresden with the help of partners from Saxony.
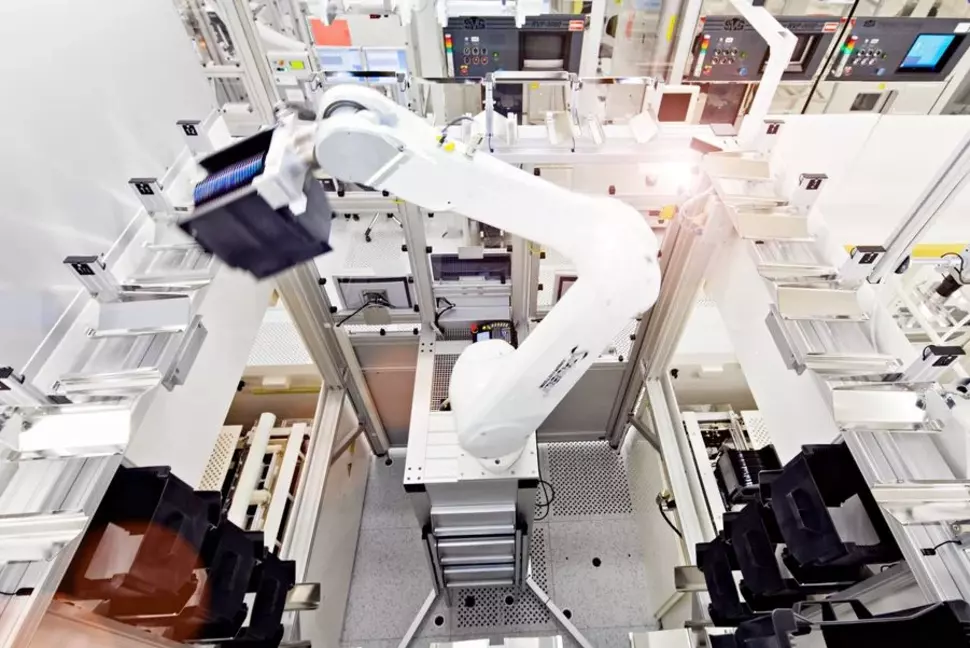
Semiconductor factories dating back to the 1990s, which have been manufacturing chips on comparably small 200-millimeter silicon disks (wafers) to date, have remained competitive at an international level even today - despite their long service life - because their operators have retroactively closed the automation gaps in these factories together with specialists from Dresden.
A prime example of this is Infineon Technologies Dresden’s cooperation with Fabmatics, Wandelbots, and other robotics specialists. “We’ve broken new ground together,” assesses Harald Heinrich, an Infineon Dresden engineer who has co-ordinated the project for many years now. “Today, we can clearly state: This subsequent automation had a very positive impact on the location, and it will ensure our competitiveness in the long run.”
“Infineon’s courage to move down entirely new paths with us when it comes to the automation of cleanroom environments has enormously advanced the pioneering work we’ve accomplished with the automation of our 200-mm production facilities,” notes Dr. Roland Giesen, Managing Director of the Dresden-based Fabmatics GmbH. “It is also thanks to this vision and the many years of faith-ful cooperation that our robotic and smart storage solutions ‘made in Saxony’ are now doing such a successful job in chip factories around the entire globe.” Infineon itself has transferred the solutions from Dresden, for example, to its Regensburg plant.
The cooperation began already in the mid-1990s when the Siemens Group built its first chip factory in Dresden which was later outsourced to Infineon. The Fabmatics predecessor “HAP” assumed the task of designing an elevator for wafer cassettes to be used in cleanrooms. “In 2004, together with HAP, we started to consider the possibilities of automating the loading of our 200 mm line without having to build special machinery every time,” recalls Harald Heinrich. During the first phase until 2009, the partners developed and built almost 30 systems: The robots were now automatically loading those production lines which had previously required a total of three employees per day in three-shift operations. These pioneering solutions paid off very quickly: Personnel expenses decreased, work pace and machine utilization increased – and the error rate ac-tually went down in the long run as well.
The second phase between 2010 and 2016 called for more complex solutions: For every additional percentage point on the way towards full automation, the project partners had to undertake an ever increasing amount of technological effort. During this time, HAP and Ortner developed the rail-bound “HERO Rail,” the first mobile robotic solution for the semiconductor industry, as well as “HERO Fab” and “SCOUT,” the first freely moving robots. SYSTEMA GmbH Dresden adapted the requisite work-flows, Kontron AIS GmbH (Dresden) created new interfaces to the chip production facilities; yet many of these factories were not at all prepared for automation. Later on, the Dresden-based start-up Wandelbots also joined the partnership and helped con-vert one of the mobile robots with ultramodern Infineon sensor technology. Today, about 200 robots work in Dresden’s factory modules. 115 of which move on rails, a handful of them moves freely in the cleanroom, the rest is firmly fixed.
With a lot of “fine tuning,” the 200-mm modules at Infineon Dresden have now attained a level of automation of 93 percent. Thus, the cleanrooms which are partially already more than 25 years old have reached the same standard as the brand new 300-mm chip factories which go into operation with high levels of automation ranging between 97 and 98 percent. Many stakeholders of the industry sector consider the Dresden model to be a blueprint also for other microe-lectronics locations in Europe which compete with the USA, Taiwan, or South Korea. Because the increased use of robots essentially negates the relatively high labor costs in Germany. In addition, there is one reason which is particularly important in a social market economy: Infineon has implemented its subsequent automation project without any dismissals. Most of the staff members whose positions became redundant were moved into other, expanding areas. All in all, this strategy has actually safeguarded and assured value creation and employment in Saxony for a long period of time which might otherwise be realized in Asia today.