Volkswagen relies on “Autoland Saxony”
The VW Group has been involved in Saxony for over 30 years. VW is also relying on the unique expertise of “Autoland Saxony” as part of its electromobility offensive - it started in Zwickau. Today the largest and most efficient electric car factory in Europe works here.
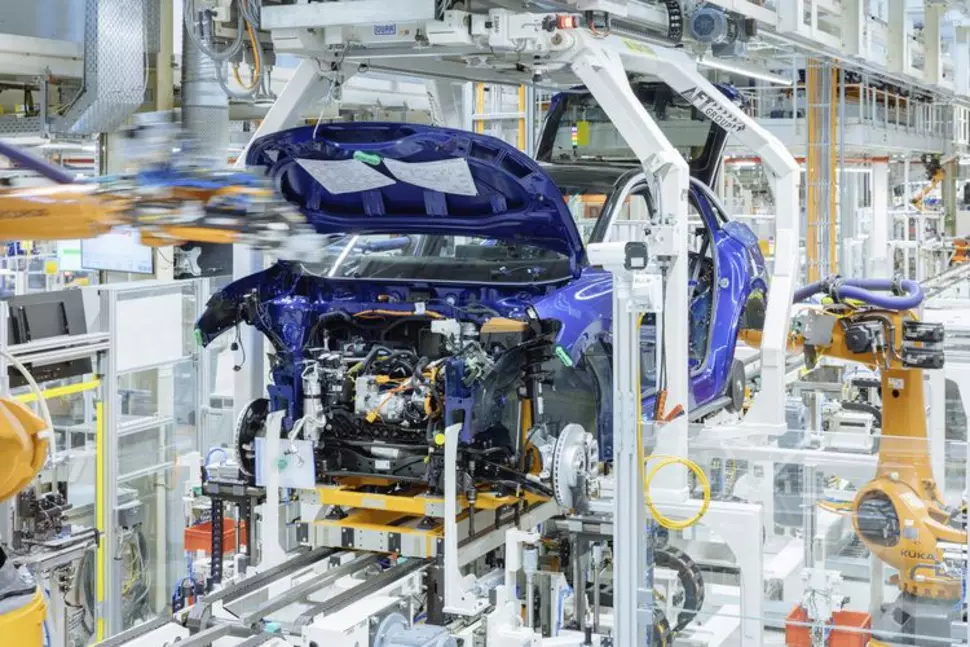
Infomodul
Facts about Volkswagen Sachsen
-
May 1990
Start of series production at the Zwickau site -
13,000 employees
in Zwickau, Chemnitz, Dresden -
> 7 million vehicles / 18 million motors
"Made in Saxony" (until 2023) -
1,300 million euros (2019 - 2022)
investment sum for the transformation of the Zwickau plant
Starting in 2033, the Volkswagen Group wants to build only e-cars in Europe. Saxony’s competences in vehicle production play a key role in this radical transformation process because what is currently the largest and most efficient electric vehicle plant in Europe is located in Zwickau. And it was actually the Zwickau vehicle plant of the Volkswagen Sachsen corporation where Volkswagen’s e-mobility campaign was launched in November 2019. The ID.3 was the first passenger car to roll off the assembly line which was built on the basis of VW’s modular electric drive toolkit (abbreviated MEB in German). At short intervals, the production start followed for such other MEB models as the ID.4 and the ID.5, the Audi Q4 e-tron and Q4 Sportback e-tron as well as the Cupra Born, the first fully electric vehicle of the Seat sub-brand Cupra.
Volkswagen Sachsen is the largest private employer in Saxony. The company employs a total of 13,000 people in Zwickau, Dresden, and Chemnitz. VW’s commitment to Saxony is of considerable significance above that: About 30,000 jobs at suppliers and service providers in the region are linked to it.
Volkswagen SachsenSuccessful Transformation
During this process, the VW plant in Zwickau evolved not only into a multi-brand production site, but also into the global lead factory for e-mobility within the corporate group.
Prior to this, a restructuring process had taken place which the persons involved compared to “changing clothes in a closet.” For the first time ever, a large automobile factory was converted completely to electromobility during ongoing operations. While in one part of the factory, Golf cars equipped with combustion engines still rolled off the assembly line, extensive rebuilding measures were undertaken in another place. The factory’s reorientation was accompanied by automation and digitalization projects with which Zwickau stands for a new era in vehicle production as well. Degrees of automation of about 90 percent in car body construction and almost 30 percent in the final assembly are top ratings for the branch. And the production also scores points with climate protection. Here, 100 percent green electricity has already been used since the end of 2017.
When it comes to the development and integration of innovative production technology, Volkswagen cooperates closely, for example, with companies in Saxony. A major research partner is the Fraunhofer IWU institute in Chemnitz.
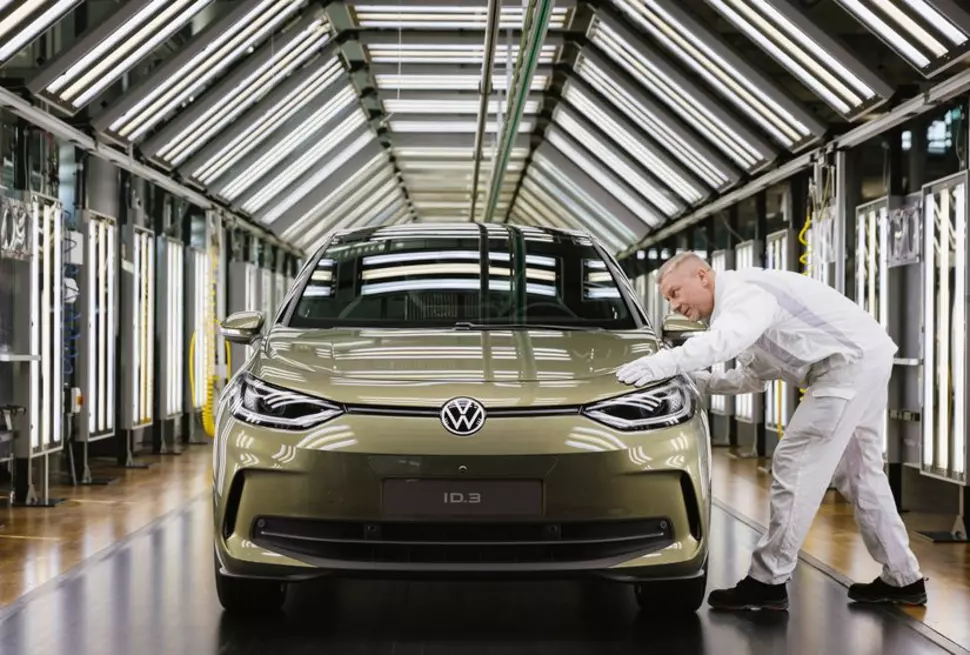
Innovative Training Strategy
The new product e-vehicle as well as the increasing degree of automation and digitalization in production also require a change in the employees’ competences. An innovative qualification strategy was introduced, in particular, by the Volkswagen Bildungsinstitut educational institute, a subsidiary of Volkswagen Sachsen which is also located in Zwickau. In the training center for the assembly of e-vehicles, the focus was not only on imparting specialist knowledge and skills, but also on emotions. In an escape room, small teams solved riddles and playfully got accustomed with the automobile production of the future. Today, the qualification concept from Saxony is also used by other e-vehicle factories of the global Volkswagen network which seek to make their employees fit for the change in production.
The competences of its employees and the transformation of the production site safeguard and assure that a current number of more than 1,400 e-vehicles leave the Zwickau plant every day – as many cars as never before in Volkswagen Sachsen’s more than 30 years of history. In addition, car bodies for the Bentley and the Lamborghini are also manufactured in Zwickau. And there is also the center for the production of special-purpose vehicles.
Milestones & Sites
The starting point for the VW vehicle production in Zwickau was on May 21, 1990. An alpine white Polo was the first vehicle to roll off the assembly line, back then still in the Trabant factory which was located in what is Zwickau’s city district of Mosel today. Already in September 1990, the cornerstone was laid for a new factory directly next door. Then and now, the reasons for Volkswagen’s commitment to Saxony were and are the same: The knowledge and expertise of the Saxony’s experts, their enthusiasm for vehicle construction as well as a business-friendly environment. All this is based on more than 120 years of automobile tradition which is characterized by continuous innovations and the willingness to change.
The first Polo and the newly built factory were followed by numerous expansions of the production site. With the pressing plant, car body construction, paint shop, and assembly unit, Zwickau grew quickly into an automobile factory spanning all production areas. By the plant’s 30th anniversary in 2020, more than six million passenger cars with combustion engines had left the factory, primarily Golf and Passat models. They are now followed by several hundred thousand all-electric passenger cars every year. By the spring of 2023, they were already more than half a million cars.Volkswagen Sachsen cooperates closely also with the City of Zwickau on the topic “sustainable mobility in the city and the region.”
Electric cars are also built at VW Sachsen’s second vehicle construction site in Saxony. In the Transparent Factory in Dresden, which officially opened in 2002 and used to be the production site of the VW Phaeton, the team commenced with the production of the e-Golf already in 2017. Today, ID.3 cars are built here. A special feature of the Transparent Factory is that customers and visitors can watch the construction of the vehicles directly on site – and even help tighten the nuts and bolts at selected points of the vehicles. The Transparent Factory also houses Dresden’s largest public and partially solar-powered e-mobility charging station. There is also a cooperation with Saxony’s state capital which pursues the objective of developing Dresden into a model city for e‑mobility and digitalization.
The transition towards electromobility is to also benefit Volkswagen Sachsen’s third production site in Saxony, the engine factory in Chemnitz. The plan is to bring thermal management, which is to be newly developed, as the first product of the future to Chemnitz by the middle of the decade. Currently, the factory delivers modern, fuel-efficient cars with direct gasoline injection as well as engine components to the VW Group’s production sites around the globe. By the end of 2022, more than 18 million engines were produced in Chemnitz.
In order to safeguard and assure the next generation of skilled professionals, the company cooperates closely with Saxony’s universities and academic institutions. Dual vocational training as well as diverse continued education and training programs are provided in cooperation with the VW Bildungsinstitut. These programs are also available to other companies from the regional business community and are very popular among them.