When the Robot Becomes a Colleague in Automotive Engineering
Numerous companies in Saxony that specialize in the planning and integration of robotics into complex production systems play a part in the consistent automation of production in Zwickau.
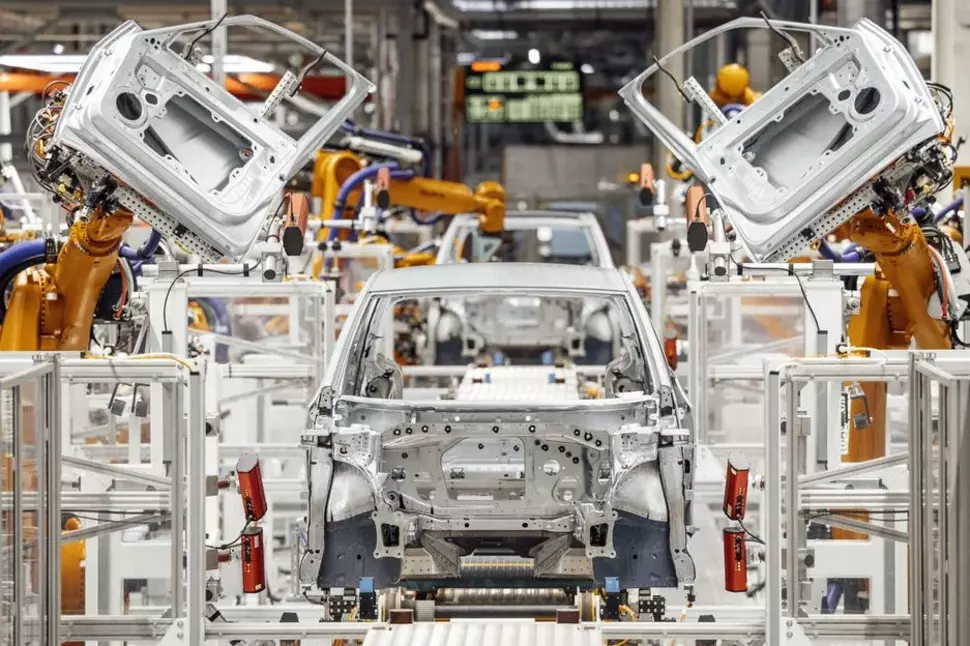
Robots have been supporting automobile production at Volkswagen Sachsen's Zwickau plant for many years.They are mainly used in the body shop and paint shop. With the conversion of the site into the first all-electric mobility factory in the Volkswagen Group, robot-based production technologies have received another significant boost - both quantitatively and qualitatively. The number of robots in the body shop, for example, has risen from around 1,300 to the current figure of 1,800. Automated high-tech solutions are also increasingly dominating the press shop, assembly and logistics. Numerous Saxon companies that understand the planning and integration of robotics into complex production systems have played a part in the consistent automation of production in Zwickau.
Fastening the underbody paneling used to be a physically strenuous task. The workers had to work overhead to screw the cover to the vehicle.Now, an assembly trolley makes this much easier. The employees place the paneling on the trolley and connect it to the hanger with the vehicle while the assembly line is running. The component is raised, several robot arms follow and screw in the screws at the designated points. The trolley then uncouples automatically and the employee drives it back to the starting point at the touch of a button. "We have implemented this fenceless assembly with lightweight robots together with the Dresden start-up Wandelbots and the Volkswagen Training Institute in Zwickau," says Lars Thielemann, Head of Planning at the VW plant in Zwickau, referring to the Saxon expertise in this pilot project.
Lars Thielemann emphasizes the new quality of robotics, which manifests itself in more flexible and space-saving applications and increasingly enables direct cooperation between humans and technology, without separating elements. This can also be seen in the adjustment and positioning of headlights during vehicle assembly. The Chemnitz-based process automation specialists at Müller & Pfeiffer GmbH have integrated an HRC application for this purpose.Saxon expertise has already been incorporated into the planning of the production processes. For example, the engineering service provider imk Industrial Intelligence GmbH from Chemnitz has contributed its expertise in the ergonomic design of modern production areas and also planned the use of robots with this in mind.
Robotics integrations "made in Saxony" can also be found in the paint shop and body shop. The already high level of automation in this area of 85 percent was increased to 90 percent as a result of the plant conversion. Companies such as IDH Automation und Fertigung GmbH Glauchau, SMA Sächsische Maschinen- und Anlagenbau GmbH Zwickau and EST Automatisierungstechnik GmbH Burkhardtsdorf have contributed to this. "Companies that we have been working well with for many years," emphasizes Lars Thielemann.A genuine Saxon innovation is used in the testing station at the end of the welding line. Here, employees control heavy industrial robots without touching them and use them to check the quality of the spot welds. The gesture control system was developed by the Fraunhofer Institute for Machine Tools and Forming Technology IWU Chemnitz.
Lars Thielemann cites Saxony's proximity to the automotive industry as a key strength in the field of automation and robotics: "The companies and research institutes know the requirements of the industry very well and have built up a great deal of expertise over the years. They know that it is important to develop solutions suitable for large-scale production from clever ideas. We remain open to this and are very interested in collaborative partnerships."